Platform Jacket Leg Internal Inspection
Scope Overview
Innovair were contracted by a UKCS operator to inspect two jacket legs on one of their assets. The aim of the visual inspections was to assess the condition of each Leg internally and perform Laser scans to identify any areas of potential concern and to create an accurate representation of the internal makeup of the Legs and associated pipework.
What did we do
Using a crawler-camera system & specialist laser scanner our inspectors successfully deployed our solutions, negotiating access challenges & internal furniture, to complete a close visual inspection & laser scan of each structure.
Innovair provided the remote visual inspection and laser scanning tools which were deployed into Legs internally. Access to the Legs were via an access hatch which have been machined just above the EL+20ft (6m LAT) level.
The tooling was manoeuvred down to the hatches on both legs using lifting equipment and deployed into the legs by Rope Access Technicians. Innovair operators conducted the inspection and laser survey from an enclosure on the +68’ deck for both legs. Both systems were gravity fed and lowered into legs in set level increments.
The close visual inspection was carried out first to ascertain initial internal configuration and this was followed by the laser survey. All data was captured successfully including inspection of external access hatches.
What were results?
Various pipework entering the leg was recorded including a layer of fluid near the bottom of the leg. Over the two-week mobilisation various datasets were collected in both legs to ascertain full understanding of leg configuration. This included high-resolution images and video of the access hatches and internal bore within the legs.
Laser Scan XYZ data was also collected within the main bore of jacket legs. Using this data, 3D models were created for the areas captured within the leg and access hatch. The laser scan data / 3D models deliver an additional advantage to the CVI data; providing a quantitative understanding of the leg access configuration and internal furniture.
Inspection reports were also generated after the scope, detailing any features, defects, their elevations, orientation and approximate size as a minimum.
What were the benefits?
Our approach focused on finding practical solutions for the project, enabling us to gather valuable data for a comprehensive understanding of the leg structure, both inside and out.
With this data, our Solutions team can now develop robotic tooling for the next phase: conducting corrosion mapping to measure wall thickness within both legs.
Whether it's modifying current equipment or designing and implementing a completely new inspection system, we are committed to delivering a solution that meets a project's unique demands while maintaining efficiency and accuracy.
Client Focal Point Feedback
"Thank you for the update and work on this project, it's been great that you managed to capture all required data."
Project Gallery
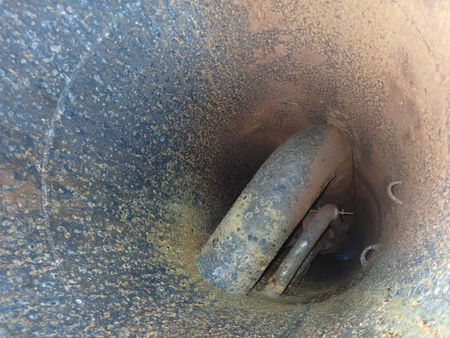

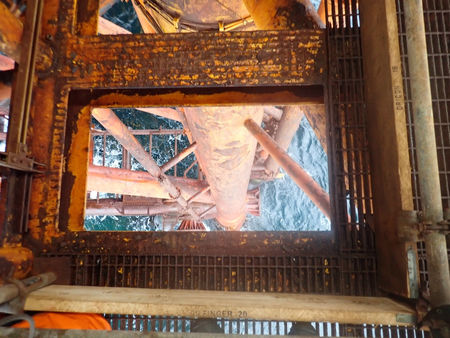