Empowering Safety through Confined Space Remote Inspections
- Innovair
- Jun 12, 2024
- 4 min read
Author: Andrew Johnston
Confined spaces present some of the most hazardous environments in various industries, from oil and gas to renewables. These areas, characterised by limited access, poor ventilation, and restricted movement, can pose significant risks to workers.
Having been involved in the energy sectors for almost 20 years, I have witnessed a changing landscape, shifting from traditional inspection methods that often required human entry into these perilous environments. Such methods exposed workers to potential hazards like toxic gases, limited visibility / emergency rescue and structural instability. However, the advent of remote inspection solutions is redefining safety protocols, offering a more efficient and, undoubtedly, safer alternative.
The Hazards of Confined Spaces
Typically defined as an enclosed or partially enclosed area with limited means of entry and exit, a confined space is not designed for continuous human occupancy, and the risks associated with entering them are numerous and significant:
Atmospheric Hazards: Confined spaces can contain harmful gases or chemicals that are not always detectable by smell or sight. Poor ventilation can lead to an oxygen-depleted environment, posing severe health risks or even fatal consequences.
Engulfment Hazards: Workers can be engulfed by materials such as liquids, solids, or flowing substances within the tank. This can lead to suffocation or drowning.
Mechanical Risks/Access: Equipment or obstacles within confined spaces may pose crushing, cutting, or entanglement hazards. This could also create poor visibility or difficult to work in conditions. Additionally, confined spaces often have restricted entry and exit points, making it difficult for workers to escape in case of an emergency or rescue operation.

Advanced Inspection Robotics: Enhancing Safety and Efficiency
Many industries now leverage advanced tools such as drones, inspection robots, ROV’s and specialised cameras to perform thorough inspections without the need for human presence. Here’s how they enhance safety and operational efficiency:
1 Eliminating Man Entry
By far one of the biggest benefits of using robotic technology for confined space inspection is we can drastically reduce or even eliminate the need for workers to enter confined spaces. This approach not only safeguards workers from potential hazards but also ensures compliance with regulatory requirements and safety standards.
2 Increased Autonomy & Data Capture
Remote technology can be equipped with high-definition cameras, thermal imaging, gas detection sensors, LiDAR and other advanced technologies. We are seeing inspection robots becoming more autonomous and capable of performing tasks with minimal human supervision. This could include the use of artificial intelligence (AI) and machine learning algorithms to enable robots to adapt to changing conditions and make decisions on their own. This enhances the speed and accuracy of inspections, ensuring that potential issues are identified and addressed promptly.
3 Cost Efficiency and Time Savings
Traditional confined space inspections often demand extensive preparation, including comprehensive safety measures, specialised equipment, and standby rescue teams. Although preparation remains crucial when planning a confined space inspection using robotic technology, the process can be significantly simplified compared to a traditional existing approach. This reduces downtime and operational costs while maintaining high safety standards.

Case Studies: Real-world Applications
At Innovair, we utilise a suite of Advanced Inspection Robotics for confined space inspection applications in a variety of industries. I have detailed some brief examples below of where we have used this technology.
Project 1: Utilising confined space drone ELIOS we inspected an offshore wind turbine foundation internally. Using drone technology meant that we eliminated man entry into potentially risky compartment of foundation where rescue would be limited.
Project 2: Using inspection crawler vehicle we inspected a clients wind turbine blades internally. Using the inspection data we can monitor the evolution of damage over time and cross reference from different blade data sources
Project 3: We conducted close visual inspections internally on 5 major condensate tanks at a site in the UK using a confined space drone ELIOS. The aim of the visual inspections was to assess the condition of each tank internally and to identify any areas of potential concern which may warrant further investigation via alternative inspection methods.
Project 4: Using confined space drone ELIOS, we inspected several Sewer lines for an infrastructure client. Data collected allowed a thorough inspection of the culvert and sewer lines and prevented any man entry.
Project 5: Utilising a bespoke magnetic crawler, we inspected oil platform jacket leg internally collecting visual and Ultrasonic C-Scan data within the structure. Access into platform leg was via a hatch located near splash zone.
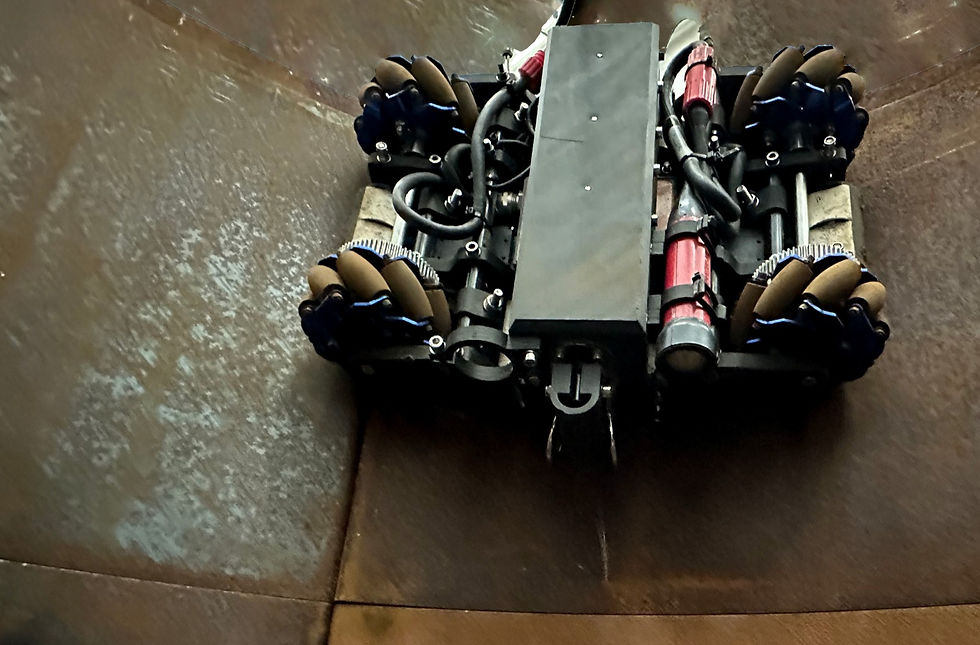
Summary
Embracing advanced inspection robotics is not just a technological upgrade; it is a commitment to the well-being and safety of workers that might be involved in confined space applications — a commitment, in my opinion, that every industry should prioritise.
The evolution of technology continues to push the boundaries of what remote inspection solutions can achieve. Emerging technologies such as artificial intelligence, machine learning in tandem with advanced inspection robotics promise even greater advancements in safety, efficiency, and data accuracy.
As these technologies continue to evolve, the potential for fur improvements in safety and efficiency is immense, promising a future where human workers are protected from the inherent dangers that a confined space could pose during an inspection.
Want more information?

A message from the author:
"Thanks for taking the time to read this blog on Confined Space Inspection. Reliable, innovative and experienced, we hope to become your go-to team for trusted inspection advice, support & solutions.
Reach out and connect with me on LinkedIn"
Andrew Johnston BEng, MInstNDT LEP
Inspection Director
Comments