3 Reasons to use autonomous drones for blade inspection
- Innovair
- Jan 17, 2023
- 3 min read
Updated: Jun 28, 2023
Author: Andrew Johnston
With the constant expansion of the wind energy network in Europe, reaching an average of 18 GW per year, asset operators are seeking ways to secure and increase the uptime and productivity of their turbines.
Blades are a vital component of wind turbines in terms of performance and overall cost of the wind power system. They are prone to damage due to their exposure to harsh environments such as rough offshore seas, course winds, freezing high altitudes, and lightning strikes, as well as defects caused by manufacturing or design issues. Due to the complexity of blade material and structure, some damages may be caused by both types of defects. When combined with repeated high loads, it's easy to see why fast, effective, and precise blade inspections are crucial to keep turbines spinning.
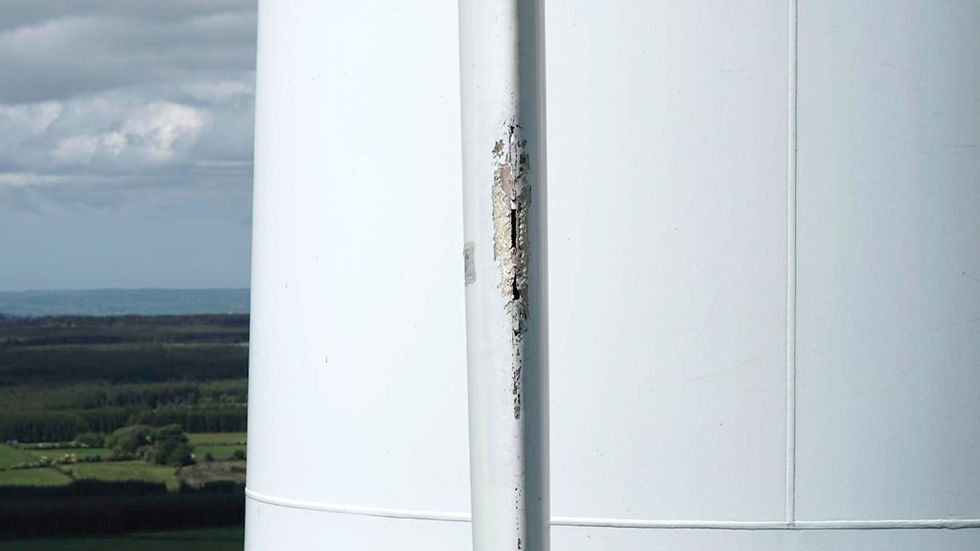
Blades are a vital component of wind turbines in terms of performance and overall cost of the wind power system
Manual drone flying has been used for many years to complete blade inspections, but as the industry has matured, the technology has evolved.
The integration of autonomous systems brings many benefits to the industry, and this blog details three compelling reasons for using autonomous drones for blade inspection.

1 100% Blade Coverage & Repeatable, Accurate Data Collection
Autonomous drones provide 100% coverage of the external blade structure by using an automated flight path that is repeated for each blade. The drone navigates around the blades at a consistent distance, using an onboard LiDAR sensor to capture accurate and high-quality, repeatable data sets for each blade inspected. This ensures that all four angles of the blade are covered without the need for pitching.
Manual drone inspections are prone to human error and safety risks, while automated flights provide the drone with situational awareness and are far more precise and accurate compared to manual flights. Even the best drone pilots may struggle to inspect a blade in the same manner as the previous flight.
2 Minimal turbine downtime for all three blades inspected
Using drones for blade inspection adds significant value by reducing downtime and costs, especially when working at heights. Replacing traditional methods like rope access or lifting aids with drones reduces inspection time per turbine, minimising production downtime. For example, shutting down a 6 MW offshore wind turbine generator (WTG) can cost approximately £5,000 in lost revenue in a full 8 hour shift.
Typically, a rope access team may inspect one turbine per day, with the turbine offline for the full shift. In contrast, an autonomous drone system can inspect all three blades on a turbine in less than 45 minutes, decreasing revenue lost due to downtime by up to 90%.
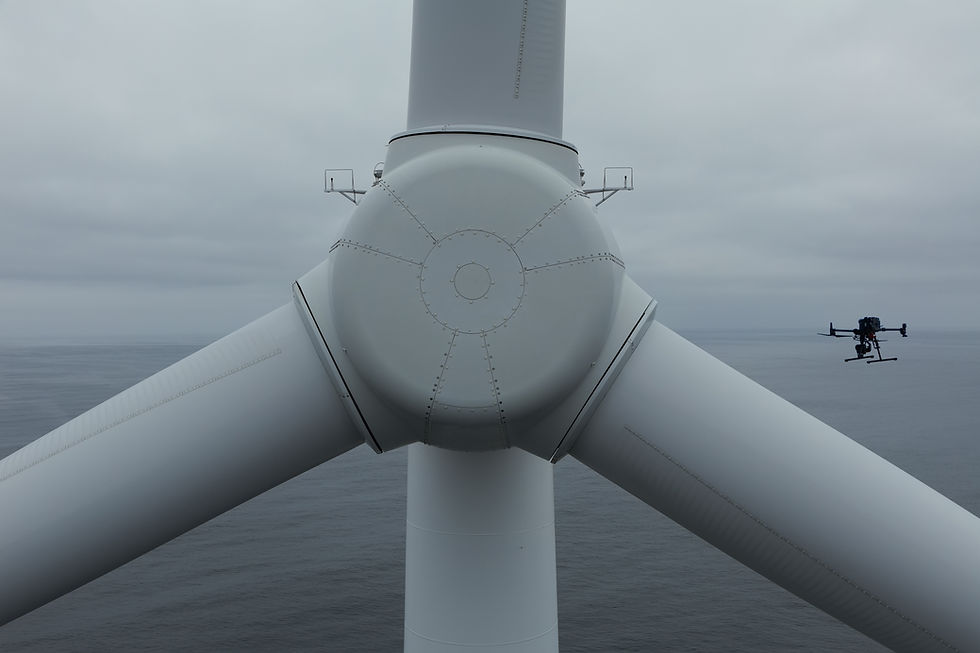
3 Less Risk than conventional inspection techniques
The use of RAS (Robotic & Autonomous Systems) can be critical in replacing repetitive inspection tasks as well as reducing health and safety risks by supporting technicians. Using autonomous drones eliminates the need for blade inspections to be carried out at height.
Repair campaigns for turbine blades, whether onshore or offshore, are not straightforward processes. The drone gathers all the data required for analysis to support repair campaigns, allowing repair teams to focus on the specific areas of repair and providing efficient operations with reduced downtime on the turbine. Working at heights carries risks in all sectors, but using this method for inspection allows for efficient and focused repair campaigns and reduces exposure for technicians working at height.
+ Summary
Blades are integral parts of the wind turbine system and frequent inspections help extend the operational lifespan of a wind turbine. Autonomous drones provide fast, accurate, and repeatable data collection while reducing exposure to working at height. These points illustrate why autonomous drones are the go-to technology for blade inspection.
Want more information?
Find out how we support our client SSE with Blade inspections every year with the following case study

A message from the author:
"Thanks for taking the time to read this blog on blade inspection using autonomous drones. Reliable, innovative and experienced, we hope to become your go-to team for trusted inspection advice, support & solutions.
Reach out and connect with me on LinkedIn"
Andrew Johnston BEng, MInstNDT LEP
Inspection Director
Comments